A dustless sand blaster is a sandblasting machine that uses compressed air to blast sand at high velocity. The dustless part refers to the machine's not creating dust, making it ideal for use in enclosed spaces or areas where dust would be a nuisance.
When working in a factory or other industrial setting, the explosion risk is not something you can ignore. Any spark can cause an explosion if enough flammable material is around.
Dust and sand are two things that any manufacturing facility will have plenty of, so reducing the risk of explosion is essential.
Thankfully, there are ways to reduce the risk of explosion while still using sand and dust to your advantage. A dustless sand blaster will allow you to use these materials without creating a dangerous environment.
Dustless sand blasters are also much safer than traditional sandblasting machines, as there is no risk of inhaling dust particles.
Read on to learn more about dustless sand blasters and their uses to decide if this could be useful at your workplace or during production in your home workshop.
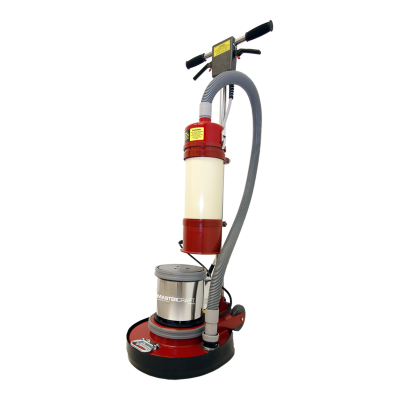
What Is A Dustless Sand Blaster?
Dustless blasting equipment is designed to make the process of sandblasting without creating lots of dust. Sandblasting is a popular way to remove rust and paint from different items, but it can be messy, dusty work.
Blasting sand and compressed air can effectively remove layers of rust and paint from items, but the dust created can be dangerous. Sandblasting without dust is a great way to remove rust and paint without creating a large number of dust particles.
Wet blasting is typically used when dust containment is required, such as in food processing plants or when cleaning delicate electronic equipment. This wet blast system can also minimize exposure to dangerous dust particles.
Soda blasting is another dustless sandblasting that uses baking soda as an abrasive material. Baking soda is a gentle abrasive that can be used on various surfaces. It is ideal for use on delicate surfaces, such as fiberglass or painted surfaces.
Why Use A Dustless Sand Blaster?
Silica dust is one of the most dangerous types of dust. Therefore, it is essential to use a dustless blaster to avoid creating this type of dust when dry blasting.
Sandblasting is a popular and effective way to remove rust, paint, and other things from materials. However, this blast cleaning method creates a lot of dust, which can be dangerous in a factory or other industrial setting with flammable materials.
Blasting with sand results in a lot of tiny sand dust particles being spread into the air, settling on flammable materials and causing an explosion.
To avoid this problem, sandblasting can be done with a dustless sandblaster and a sand nozzle. Sandblasting without creating dust is safer than blasting with sand as it will not lift off rust and paint and create a dusty environment.
Sandblasting without dust allows a gentler cleaning process than blasting with sand. It also allows for more controlled cleaning. Sandblasting without dust provides for a more controlled and more delicate cleaning process.
APPLICATIONS OF DUSTLESS SANDBLASTING
Dustless sandblasting can be used for a wide range of applications, both in residential and commercial settings. Here are some examples:
-
Removing paint, rust, or other coatings from metal surfaces, such as cars, boats, or industrial equipment.
-
Cleaning concrete, brick, or stone surfaces, such as driveways, sidewalks, or buildings.
-
Removing graffiti from walls or other surfaces.
-
Preparing surfaces for painting, staining, or sealing.
-
Restoring old furniture, such as chairs, tables, or cabinets.
-
Getting rid of stains or discolorations from pool decks, patios, or pavers.
-
Cleaning mold, mildew, or other contaminants from surfaces.
Types Of Dustless Sand Blasters
A dustless blasting machine has several types for different applications. There are two main types of dustless sandblasters to be aware of. These are the cyclonic sandblaster and the rotary sandblaster.
Cyclonic Sandblasters
Cyclonic sandblasters are designed to produce a clean stream of sand. They work by using a cyclone to separate the larger debris from the sand, and then the sand is fed through a filter that catches the smaller particles.
Rotary Sandblasters
Rotary sandblasters use a rotating barrel to create a sand slurry and force the mixture through an air or water nozzle. Rotary sandblasters can also pump air out of the sand slurry as it travels through the barrel. This air acts as a secondary cleaning method.
How To Use A Dustless Sand Blaster
These machines work by mixing water and abrasive material in a blaster gun. The mix is then blasted at high pressure onto the surface that needs to be cleaned. The water helps to cool the surface as it is being cleaned and also reduces the dust created by the sandblasting process.
Dustless sand blasters are easy to use. First, fill the blaster with the appropriate sand and add water to the nozzle. The water will help to create a slurry that can be quickly blasted onto the surface.
Once the blaster is filled, aim it at the surface and pull the trigger. The dustless sand blaster will do the rest.
Blasting without dust is done with the help of a sand nozzle. The nozzle is a device that mixes compressed air from the sandblaster with the sand.
The two materials are combined into a slurry that is then shot onto the item being worked on. The blasting process usually only takes a few minutes, and the results can be impressive.
Uses For A Dustless Sand Blaster
Traditional blasting methods could potentially be dangerous as they create a lot of dust. In that case, a dustless blaster is great for cleaning materials without creating dust. However, they can also be used to blast materials.
Metal Surfaces
Dustless sandblasters can be used to blast materials like old paint and rust off of metal surfaces. They can also be used to blast away other materials such as asphalt.
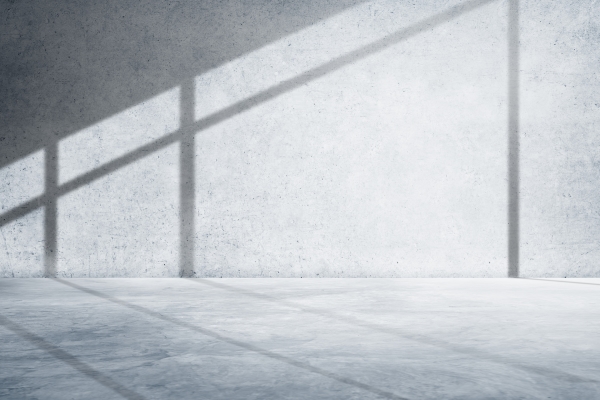
Concrete
Dustless sandblasters can also blast materials such as paint off concrete and other surfaces.
Roofing Tar
They can also blast away other materials such as roofing tar. If a sand blaster is being used to blast materials, it is crucial to ensure that it is set up correctly.

When Should You Use A Dustless Sand Blaster?
Dustless sandblasters are great for when you want to blast materials without creating dust. Sandblasting is a popular method for removing old paint and rust from items.
However, the dust created by sandblasting can be dangerous in a factory or other industrial setting. The blasting system should be set up in a dust-free area.
Dry blasting is a process that uses compressed air to blast away materials. The material being blasted is typically in a dust form. The dust collector then collects the dust.
This is a gentler cleaning method than using a power sander. When sandblasting without dust, a sandblaster needs to be used. This can be used to clean old paint and rust from items.
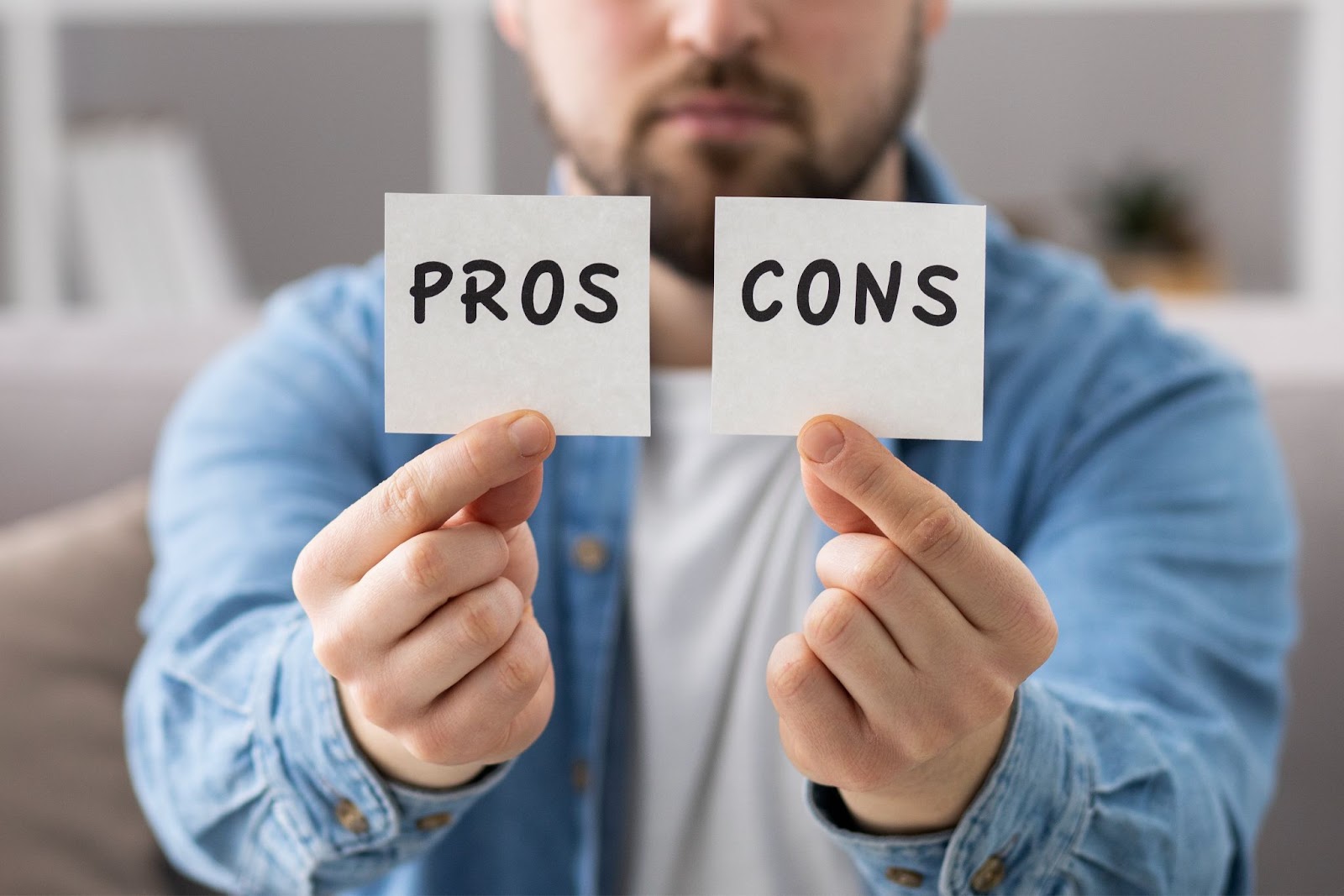
Pros And Cons Of Using A Dustless Sand Blaster
Before using a dustless sand blaster, weigh the pros and cons. Consider whether or not the dustless sand blaster is necessary for the job at hand.
Pros:
- Dustless sandblasters are easy to use
- Dustless sand blasters create a slurry that can be quickly blasted onto the surface
- Dustless sand blasters allow for more controlled cleaning
Cons:
- Dustless sandblasters can be expensive
- Dustless sandblasters may not remove all of the debris from the surface
In some cases, a dustless sand blaster may be the best option. In other cases, a power sander may be a better option. Choose the sand blaster that works best for your task.
Dustless blasting is a great way to blast materials because you can use lower pressure than you would need to blast materials with sand. This means that the cleaning will be gentler.
This can also be a more controlled cleaning process because you can control the airflow more easily. It is also easier to use blast nozzles than it is to use a sandblaster with no sand nozzle.
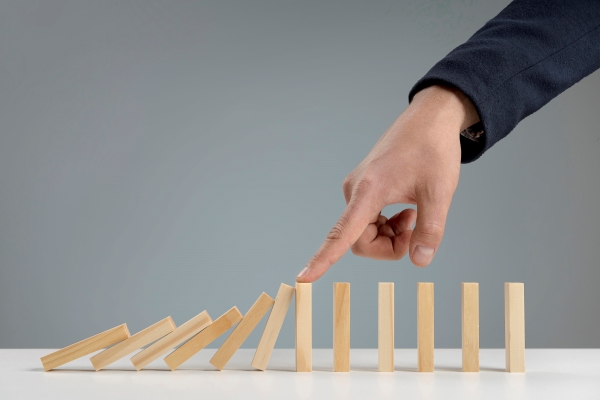
How To Reduce The Risk While Using A Dustless Sand Blaster?
There are a few ways to reduce the risk while using dustless blasters.
First, always wear gloves when handling the blaster. The blast media also needs to be properly wetted down before use. Abrasive media may also be used with dustless sandblasters but should be used with caution.
Second, be sure to keep the area well ventilated. This will help to reduce the amount of dust that is created.
Third, use a dust mask when operating the machine during the sandblasting process. This will reduce the amount of dust that is inhaled.
Fourth, use a dust collector when using the dustless sandblaster. This will help to collect the dust that is created.
Fifth, always clean up after using the dustless sandblaster. This will help lessen the amount of dust that is left behind.
While a dustless sand blaster is a better option than a sandblaster, safety precautions can be put in place to reduce the risk of explosion further.
It is also essential to ensure that the materials close by are not flammable. This includes the surrounding walls, the flooring, machine parts, and other parts of the production area.
Conclusion
Sand particles in an industrial setting can be dangerous. A dustless sand blaster can help reduce the amount of dust created.
When it comes to industrial cleaning and safety, you must decide the best way to clean your equipment as a business owner. Many dustless products on the market can save time and money and are sustainable.
If you have a dust problem, the dustless sand blaster is the best option for you.
0 comments